ACTIVATED CARBON TOWER
PROCESS DESCRIPTION
흡착탑(Activated Carbon Tower)이란
각종 유기성가스 및 악취를 물리, 화학적 방법으로 흡수, 흡착하는 방지시설로써 활성탄 표면에 있는 원자의 자유결합과 가스성상에 따른 화학적 결합력으로 제거된다.
대부분 저농도 발생가스일 경우 적용가능하며, 일정한 흡착제를 사용하면 타겟물질을 선택적으로 제거할 수 있기 때문에 산업분야 및 환경방지 설비등에 광범위하게 활용되고 있다.
흡착제(활성탄,실리카겔등)는 다공성(Porous) 이고 모세관이 많을수록, 흡착 물질에 대한 친화력이 클수록 흡착효과는 커진다.
흡착제의 종류와 용도
흡착제 |
용도 |
활성탄(Activated carbon) |
용제회수, 악취제거, 가스정화(가장많이 사용) |
알루미나(Alumina) |
가스, 공기 및 액체의 건조 |
보오크사이트(Bouxite) |
석유류의 유분제거, 가스 및 용액의 건조 |
본차(bone char) |
설탕의 탈색 |
탈색카본(Decoloring carbon) |
기름, 색소, 유분 및 왁스분제거, 음료수 탈색 |
훌러스어스(Fuller's earth) |
윤활유, 지방 왁스의 정제 |
마그네시아(Magnecia) |
휘발유, 지방 왁스의 정제 |
실리카겔(Silicagel) |
가성소오다 용액중 불순물 제거 |
황상스트론티움(Strontium sulfate) |
가스의 건조 및 정제, 가성소오다 용액내의 철분제거 |
활성탄의 종류와 특성
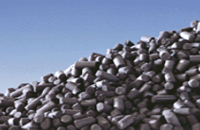
Figure3. constructed carbon
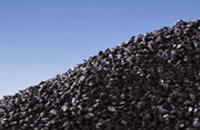
Figure4. granular active carbon
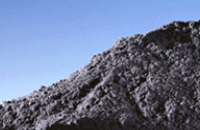
Figure5. powdered active carbon
- 조립 활성탄(Constructed carbon)은 고가이지만 높은 흡착율을 보여 고농도의 가스처리에 주로 이용된다.
- 입상 활성탄(Granular or pelletized active carbon)은 충분히 넓은 표면적을 갖고 고장성(fixed bed)에서 압력 강하가 적으며 흡착된 물질을 비교적 쉽게 회수할 수 있어 가장널리 사용되고 있다.
- 분말탄(Powdered active carbon)은 값은 싸지만 입상탄보다 질이 떨어지고 충전탑에 사용할 때 압력강하가 너무 크기 때문에 사용에 많은 제한이 있다. 또한 분말탄은 거의 재생할 수 없어 사용 후 폐기하여야 한다.
전자현미경 사진으로 본 입살활성탄 세공
벌크 밀도(bulk density) |
22-34lb/ft² |
열용량(hear capacity) |
0.27-0.36Btu-lb℉ |
공극 부피(pore volume) |
0.56-1.20㎤ / g |
표면적(surface area) |
600-1600㎠ / g |
평균 공극 직경(average pore diameter) |
15-25 |
재생온도(regeneration temperature:steam) |
100-140℃ |
최대허용온도(maximum allowable temp) |
150℃ |
활성탄의 악취성분별 흡착능력
흡착탑 운영
흡착공정은 3단계 공정으로 이루어지는데 먼저 유체(기체)가 흡착제에 접촉하면 선택적으로 흡착제에 기체가 흡착된다. 이후로 흡착되지 않는 유체가 흡착제-흡착질과 분리되어 나가고, 마지막으로 흡착제는 흡착한 가스를 처리(탈착) 하여 재생하거나, 사용된 흡착제를 버려 새로운 흡착제로 대치 한다. 대부분 산업용 흡착공정에 서는 흡착이 끝난 다음 흡착제를 탈착하여 다시 사용한다.
탈착에 의한 흡착제의 재생(regeneration)은 흡착제의 성질에 따라 여러 가지 방법이 있는데, 보통 가스나 증기를 탈착 할 때는 흡착제-흡착질의 온도를 올리거나 (열순환:pressure cycle)으로서 이루어진다. 아주 보편적인 열순환 방법은 뜨거운 가스를 흡착층에 통과시켜 나오는 기체를 냉각하고 분리공정에서 가스를 회수한다.
Activated carbon tower 종류
1. 고정층 흡착장치(fixed bed adsorber)
흡착탑은 보통 원통형 용기를 쓰며, 입상의 흡착제를 충진하고 흡착제(활성탄)을 유지시키기 위하여 스크린(Screen)을 설치한다. 흡착조 수직과 수평으로 이용하는 2가지 경우가 있는데 대량의 가스를 처리하는 경우에는 수평 흡착탑을 주로 쓴다. 또한, 유입가스를 연속적으로 처리할 경우에는 흡착탑 2기를 병렬로 연결하여 흡착 및 재생을 교대로 실시한다. 보통 단면속도는 9-30m/min, 체류시간은 0.6-6초로 설계한다.
2. 연속 흡착장치(Continuous Adsorber, 이등층 흡착기)
연속 흡착기의 대표적인 구조는 그림과 같이 활성탄상을 회전하는 이중통으로 되어 있다.
흡착제는 연속적으로 흡착부에서 탈착부로 이동해서 탈착되며, 항상 포화된 흡착제를 탈착부로 이동시킬 수 있고, 단시간에 회전되므로 흡착제(활성탄) 사용량이 적게 든다.
3. 유등층 흡착장치(Fluidizing adsorber)
흡착제의 유동층에서 흡착을 행하는 방식으로 가스의 유속을 위의 2가지 방식보다 크게 할 수 있고 상대적으로 압력손실이 적다. 또한 고체와 기체의 접촉도 잘 된다는 장점이 있으나 흡착제 입자의 유동으로 마모가 크다는 단점이 있다. CS2를 회수할 때 이 방식을 이용한다. 회수율은 90-95%정도 이다.
파과점
혼합가스를 활성탄에 투과시키면 초기에는 흡착율이 매우 높으나 시간이 지날수록 흡착율이 떨어져 점차 출구가스에 증기성분이 서서히 나타나기 시작하는데, 출구가스에 증기성분이 나타나기 시작하는 이점을 활성탄의 파과점이라고 한다. 흡착공정에서 파과점을 지나면 흡착효율은 전차 감소한다.
이때 흡착기 출구 처리가스 중 흡착되어야 할 증기가 나타나는 점이 파과점이며, 흡착기 입구와 출구에서 증기의 농도가 같아질 때를 활성탄이 포화 되었다고 한다. (Figure 8. breakthrough curve 참고)
Figure 8. breakthrough curve
흡착탑 화재 방지기술
- 1발화온도는 야자각 활성탄이 약 200℃, 석탄계 활성탄이 약 350℃이므로 석탄계 활성탄이 유리하며 축열에 의한 발열을 피할 수 있도록 형상이 균일한 조립상 활성탄을 사용한다.
- 2Dead Zone이 있으면 축열이 일어나므로 활성탄층의 구조를 수직 또는 경사지게 하거나 활성탄 층의 두께(높이)를 0.5m 이하로 설치한다.
- 3접촉 시간을 2 sec이하로 한다. 즉 선속도를 0.2m~0.4m/sec로 한다. 선속도가 0.2m/sec미만이면 유속이 낮아 축열가능성이 있음.
- 4흡착탑 전단에 Wet Scrubber나 Heat Exchanger를 설치 또는 공기와 희석하여 온도를 70℃이하로 한다.
- 5운전 초기에 흡착열이 발생하여 15~30분 후에는 점차 낮아지므로 물을 충분히 뿌려 주어 30분 정도 공기를 공회전 시킨 다음 정상 가동한다. 초기에 첨가된 물은 가동 중 자연히 탈착되며 활성탄의 흡착능력을 감소시키지 않음.
- 6흡착탑에 열전대 및 온도 감지 경보시스템(상한선 100℃ 또는 운용 환경에 따라 조정)을 설치하여 온도 상승시 Water Spray되도록 안전 장치를 설치한다.
- 7운전 정지시 유입가스를 온도가 낮은 공기로 전환시키고 송풍기를 30분 정도 공회전 시켜 흡착탑 내부 온도를 50℃이하로 낮춘 다음 운전을 종료한다.